Magnetic Particle Inspection (MPI)
Simple and compact, this method of non-destructive testing can go just about anywhere. Detect surface flaws, manufacturing defects, and minor sub-surface flaws in your equipment quickly and efficiently with magnetic particle inspection.
Magnetic Particle Inspection
You might miss surface cracks or defects in your equipment until it's too late. Magnetic Particle Inspection (MPI) is a cost-effective and straightforward non-destructive testing (NDT) method. It works well on various materials, including new welds, castings, and materials in use. Whether it's after machining or grinding, MPI helps ensure there are no new defects in your assets or equipment. By identifying both manufacturing and in-service defects, you can ensure your equipment is safe for your employees before putting it to work.
How it works:
Magnetic Particle Inspection (MPI) is straightforward to interpret but has some limitations. It's effective at detecting surface or shallow subsurface flaws. Magnetic Particle Inspection allows Anode NDT to create a magnetic field on a material's surface. We sprinkle it with iron particles; these particles are drawn towards any magnetic field leaks caused by defects like cracks. This approach uncovers flaws on or just below the surface, which might be invisible to the naked eye.
Equipment Requiring Magnetic Particle Inspection:
Pressure Vessels
Industrial Facilities
Custom Fabrication
Bridges
Pipelines
Overhead Lift Equipment (Cranes, Boom Trucks, Side Booms, Manlifts)
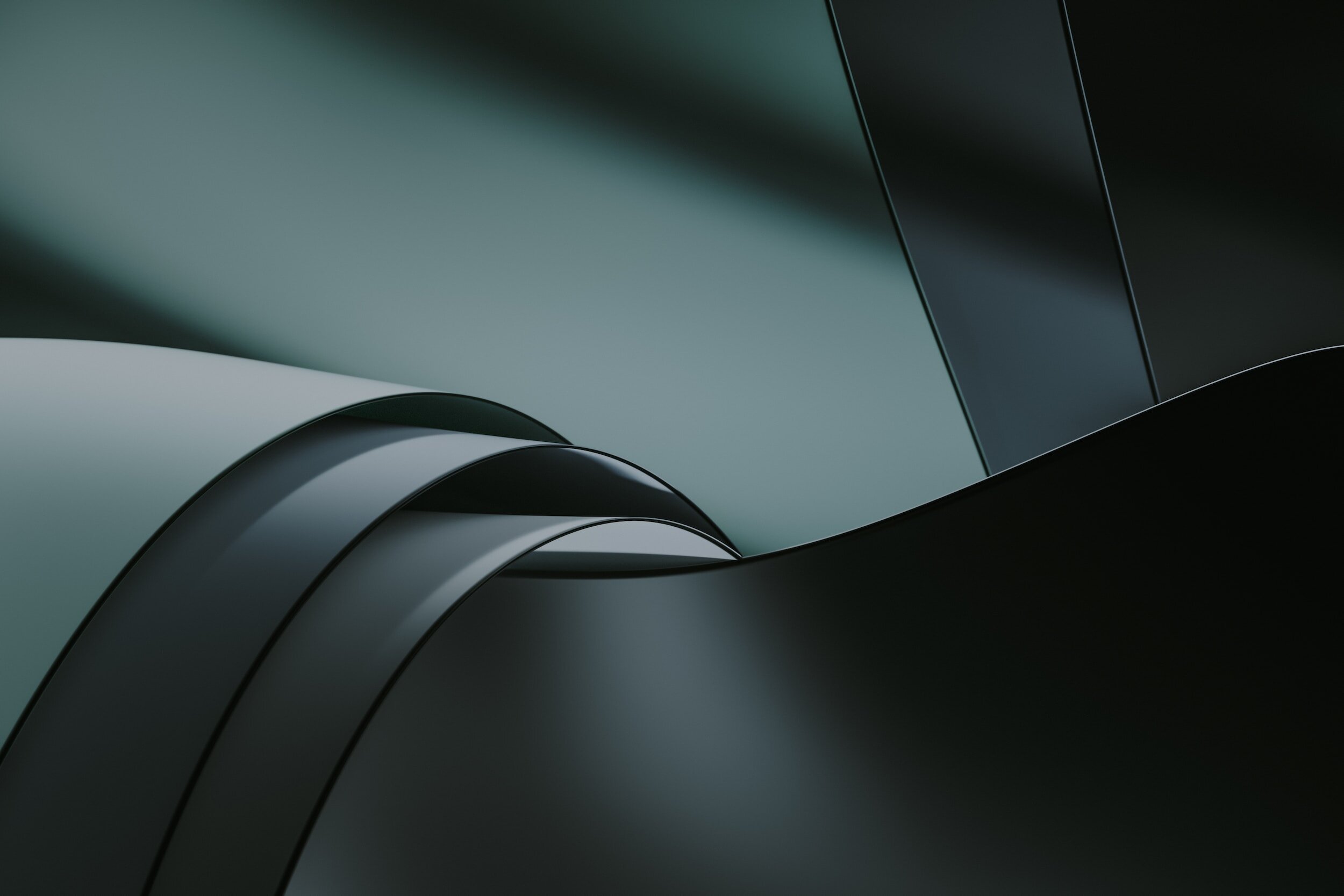
We Meet and Exceed Safety and Code Compliances
Safety is paramount to Anode NDT: both our technicians and our procedures prioritize efficiency and safe work practices.
All Anode NDT procedures are ABSA demonstrated and backed with CGSB / ASNT Level III certified support.
We proudly hold ASNT Level II certification.
Our in-house safety program is ISNetworld, ComplyWorks, Avetta, and COR compliant.